
Repair Services
When your electric motor or generator fails, it can be disruptive both financially and operationally. Repairs must be made as quickly as possible to maximize your process uptime and reliability. This is where Scott Armature excels – fast turn arounds are our business and the basis for our reputation in the electro-mechanical repair industry. Furthermore, the repairs will meet or exceed ISO 9001 and EASA Quality Standards assuring our customers of the highest quality repairs, on time, and within budget.
Rewind and Recondition (up to 13.8kV)
Recondition Scope of Work
- CHECK AND RECORD THE OUT-PUT SHAFT / COUPLING FOR RUNOUT
- CHECK AND RECORD THE ROTOR END FLOAT
- DISMANTLE MOTOR
- CHECK AND RECORD ALL APPLICABLE MECHANICAL FITS
- STEAM CLEAN AND BAKE ALL WINDINGS
- DIP AND BAKE WINDINGS
- DYNAMICALLY BALANCE THE ROTATING MEMBER.
- CLEAN AND PRIME ALL METAL PARTS.
- ASSEMBLE MOTOR
- TEST AND RECORD BEARING / HOUSING INSULATION
- BLUE CHECK THE SLEEVE BEARINGS FOR SHAFT CONTACT AND ALIGNMENT
- CHECK AND RECORD SHAFT / COUPLING RUNOUT
- CHECK AND RECORD ROTOR END-FLOAT
- CHECK AND RECORD FACE AND RABBET RUNOUT ON VERTICAL MOTORS
- PERFORM ELECTRICAL TEST, DAR OR PI AND DC HIGH POTENTIAL TEST
- TEST RUN MOTOR RECORDING THE ESTABLISHED BEARING TEMPERATURES, IDLE CURRENT AND VIBRATION LEVELS
- TEST ALL ACCESSORIES
- COMPLETE AND PAINT MOTOR
Up to 13.8kV Rewind and Reconditioning Services

Rewind Scope of Work
- CORE LOSS TEST PRIOR TO STATOR BURNOUT
- PARTS PLACED IN OVEN AND SUPPORTED TO AVOID DISTORTION
- CORE SLOTS CLEANED
- CORE TEETH NOT SPLAYED
- CORE LOSS TEST AFTER STATOR BURNOUT
- CORE LOSS DIMENSIONS ARE EQUAL FOR BOTH READINGS
- MAGNETIC FLUX IS WITHIN 2% OF EACH TEST
- CORE LOSS CHANGE LESS THAN 20%.
- INFRA-RED HOT SPOT TEST PERFORMED
- WINDING DATA CAPTURED AND SUBMITTED TO COIL VENDOR
- EASA DESIGN VERIFICATION
- RTG READING INCLUDING TEMPERATURE
- WIND STATOR
- DC HI-POTENTIAL TEST CONNECTED WINDING
- SURGE COMPARISON TEST CONNECTED WINDING
- DLRO OR SPIN TEST
- PRE-HEAT WINDING BEFORE VPI OR VARNISH DIP
- PROCESS COMPLETED WINDING IN VPI SYSTEM (SEE VPI)
- CURE VPI’D STATOR IN BAKE OVEN
Rewinding and Connecting 6000HP Stator
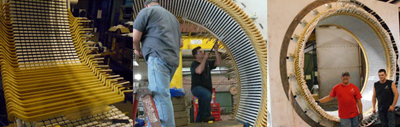
Coreloss Testing
Core loss testing has become essential in ensuring quality electric motor and generator repairs. The stator lamination is tested to determine the watts loss per pound of steel magnetic core iron. When electric motor & generator windings fail, they often damage the stator lamination. This causes hot spots to develop leading to premature winding failures. If your company has had an electric motor or generator repaired only to have the machine run hot and burn up after a short operating time, the most likely cause was a damaged stator lamination core. This problem will no longer be a cause of concern when this test is performed.
Dynamic Balancing
Dynamic Balancing Of Shafts And Rotors Up To 25,000 lbs.
InstrumentationBalancing specifications are computer controlled using ENTEK/IRD 290T instrumentation equipment. This insures precise tolerances no matter how special your requirements may be.
” IF IT ROTATES WE CAN BALANCE IT “
Laser Alignment
ROTALIGN PRO the most versatile laser shaft alignment system:
• Soft Foot Wizard for detection, measurement and correction.
• Machine Train Alignment of up to 6 machines complete with tolerances, targets. etc.
• Long Range: Easily accommodates a 33 ft. measurement separation between laser and receiver.
• Monitors horizontal and vertical moves live and simultaneously.
• Optimal move feature graphically displays best combination of moves for bolt-bound situations (move motor, pump or both).
• Direct entry of target specifications, or thermal growth values at the feet. Thermal growth computation.
PDMA Analysis
PdMA – MCE Offline Testing
Surge Comparison Testing
Digital Surge Tests Performed:
• Resistive Imbalance
• Inductive Imbalance
• Resistance to Ground (“RTG”) Reading
• Capacitance to Ground (“CTG”) Reading
• Polarization Index and Dielectric Absorption
• Step Voltage TestTesting Surge testing of A/C electric motors and generator windings displays a accurate picture of the winding and insulation conditions. Tests made can determine good, marginal or defective windings and the winding insulation before a major failure occurs. In many cases actions can be taken to head off these failures, preventing costly delays and repairs. This digital surge tester applies a predetermined voltage and captures a sinusoidal wave form for each phase of the unit under going the test. It also displays megohms and Hi-Pot measurements. All the information is used to make the correct decision on what repairs are needed.
This is a Surge Test:The wave form showing a good winding. You will notice how each of the three phases overlap each other. Representing what appears to be only one wave line. Pictured is the windings that are being tested, no faults are present.
Turn to Turn / Phase to Phase Weakness: If there is a Turn to Turn / Phase to Phase weakness The wave patterns will separate and appear unstable This is an indication of imminent failure. The motor should be serviced immediately. Pictured is a turn to Turn / phase to phase fault.
Ground Faults: If there is weak insulation the wave pattern will indicate the weakness. If a motor with a turn to turn fault short stays in service circulating currents may produce hot spots and the ground wall insulation will eventually burn up causing a shut down. Pictured is a ground fault.
Vibration Analysis
The CSI 2130 Machinery Health Analyzer is part of Scott Armature’s complete range of monitoring services to all industry segments. It is a full featured portable data collector & analyzer designed in a small lightweight package that monitors the condition of rotating equipment found in many process industries such as power generation, petrochemical, pulp and paper, and primary metals. The 2130 collects field data, including vibration information and process variables, next collected data is uploaded into our computer, analyzed to determine the defects and make recommendations to correct the problems.
VPI Processing
9′ Imprex VPI System
VPIVacuum Pressure Impregnation (VPI) has been used within the electrical industry for many years. VPI was first used as an improved method of forcing resins through multiple layers of wire and insulation. Over the past three decades a majority of original equipment manufacturers have utilized VPI processing to improve the performance and life of industrial duty electric motors. Electrical apparatus treated by the VPI method have proved so successful that it is becoming increasingly specified by the military, steel, and electrical generating companies for severe duty applications.
Vacuum Pressure Impregnation offers several features that help prevent the primary causes of motor and generator failure.
INSULATION VOIDS are eliminated through the use of the VPI process. Voids may contain moisture, dust, or other contaminants which lead to a much shortened insulation life. Voids are common place for corona to occur in high voltage applications. The VPI process is the best means of obtaining a void free system.
PREMATURE THERMAL AGING is greatly reduced by the excellent heat transfer properties offered by VPI Systems. Small air pockets in coils, or between coils and core iron, reduces heat transfer. Heat that cannot escape from the coil to the iron will greatly decrease the life of the insulation system.
VIBRATION is practically eliminated with VPI. An energized coil will move and cause abrasion of insulation unless securely anchored. The complete saturation of insulation and support material results in a solid mass that prevents coil movement.
RESIN Description
PEDIGREE No. 4000F HERMETIC CO-POLYMER INSULATING RESIN
PedigreeTM No. 4000F Hermetic Co-Polymer Insulating Resin has been formulated as a more
flexible version of the standard 4000 Polymer. It was formulated for (VPI) vacuum pressure
impregnation applications, but is also suitable for dip and bake operations.
APPLICATION
• VPI, Dip and Spin or Static Dip and Bake impregnation of motors, coils, and stators
RELATIVE ADVANTAGES
TYPICAL USES AND PROCESSING
Motor Load Testing
1500 HP Load Testing Dyno
1500 HP Taylor Dynamometer Spec Sheet
Load Testing Capabilities:
• AC: up to 1500 HP
• DC: up to 1200 HP
• DC: up to 1200 AMP – 750 V Armature
• AC: 480 V – 13.8 KV
• Up to 8000 HP Full Voltage (no load)
• 8750 Ft-Lbs Maximum Measured Torque
• Locked Rotor as Per IEEE 112 Reduced Voltage Locked Rotor Test 5.9.2.1
• Speed, Torque & Current Curve
• 300 – 4000 RPM
• Efficiency
• Water-Cooled Motors
• IEEE 112 & 115 Standard Testing
• Generators up to 5MW Open Circuit / Short Circuit Testing
• ABS Testing
• UL Testing
Technical Resources
EASA Mechanical Reference Handbook
Reproduced from Mechanical Reference Handbook Copyright 1999, Electrical Apparatus Service Association. All Rights Reserved.
Oil & Grease | Alignment | Balance & Vibration |
Sleeve Bearing & Seal Clearance | Belt Installation | Belt & Sheaves |
Belt Tensioning | Oil & Grease Compatibility | Terms Glossary |